The world is racing towards electric and hybrid light vehicles. This transition brings benefits across the local, regional and global scale. But lithium car batteries don’t last forever: they have a life span of between 5 to 8 years or 60,000 to 100,000 miles. This poses the question: can recycling lithium car batteries be done?
In short, yes, it can. As of 2022, the world recycles around 1,000,000 tons of lithium batteries annually.
In this article, we’ll explore how to recycle and reuse lithium car batteries.
Table of Contents
Why Recycle Lithium Car Batteries
Lithium battery recycling has grown significantly in the past few years. Strong demand for minerals, and the tight global supply, have driven this growth.
Recent increases in commodity prices have also encouraged recycling because recycled batteries are cheaper than mineral ore. They are also richer in suitable metals. For example, the average cobalt content of spent battery electrodes can be around 20% by weight; this is much higher than in natural ores and shows the attractiveness of recycling.
In addition, according to forecasts, demand for lithium will be 2 to 6 times greater than global mineral deposits by 2040. Therefore, raw mineral supplies will not be able to meet the demand.
With this in mind, economies that don’t recycle lithium car batteries will be at a severe disadvantage. For this reason, recycling lithium car batteries has strategic economic importance to countries moving to electric transport.
What Are Lithium Car Batteries Made Of?
How Do Lithium Car Batteries Work?
Firstly, we’ll cover some technical basics before we dive into how recycling works.
Lithium car batteries store the electrical energy that drives an electric vehicle. They do this by storing electrical energy at a chemical level. In essence, the location of mobile lithium ions is how batteries store energy; when the battery charges or discharges, the ions move.
Therefore, an electric ‘push’ is the only way to move lithium ions. For this reason, your car battery has a positive and negative terminal. This is mirrored inside the battery by the oppositely-charged anode and cathode, shown in the diagram below. These electrodes attract or repel the lithium ions depending on the charge cycle.
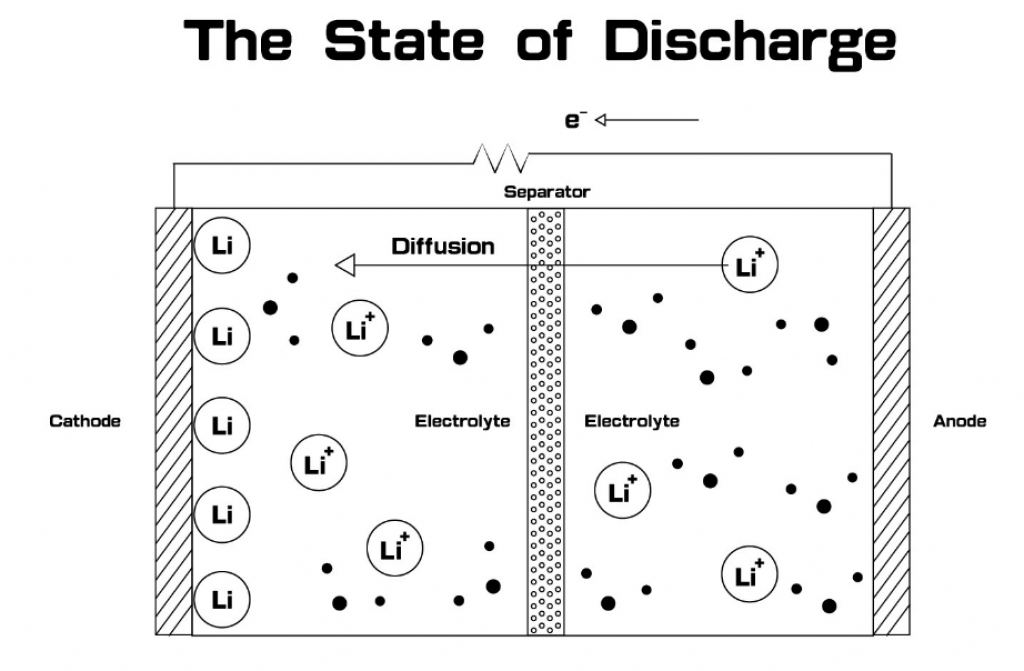
Source: hopaxfc.com
When the battery discharges, a switch connects the electrical circuit between the positive and negative terminals. This connection pushes lithium ions from one side of the battery to the other. The flow of ions causes a flow of electrons, i.e., electricity. Thus electricity flows through the wires coming out of the battery.
When you charge a battery, you’re applying a voltage to the terminals of the battery. This voltage causes the reverse of the discharging process. The electrical pressure (i.e., voltage) forces the lithium ions to migrate back to the other side of the battery.
Finally, a separator divides the battery and prevents leakage, thereby stopping lithium ions from wandering by themselves.
An Analogy
Here’s an analogy to illustrate how batteries work:
Imagine two factories and a group of workers. The factory workers (mobile lithium ions) can choose to work at one of the two factories (the cathode or the anode). The workers will “change jobs” and move from one factory to another when the “pay” is better at the new factory.
In our analogy, the pay is the electrical pressure that attracts the lithium ions to cross over from one side of the battery to the other. In the same way, if the pay gets better at the other factory, the workers return.
Design Of Lithium Car Batteries
Firstly, like with any engineered technology, many components go into a lithium car battery pack.
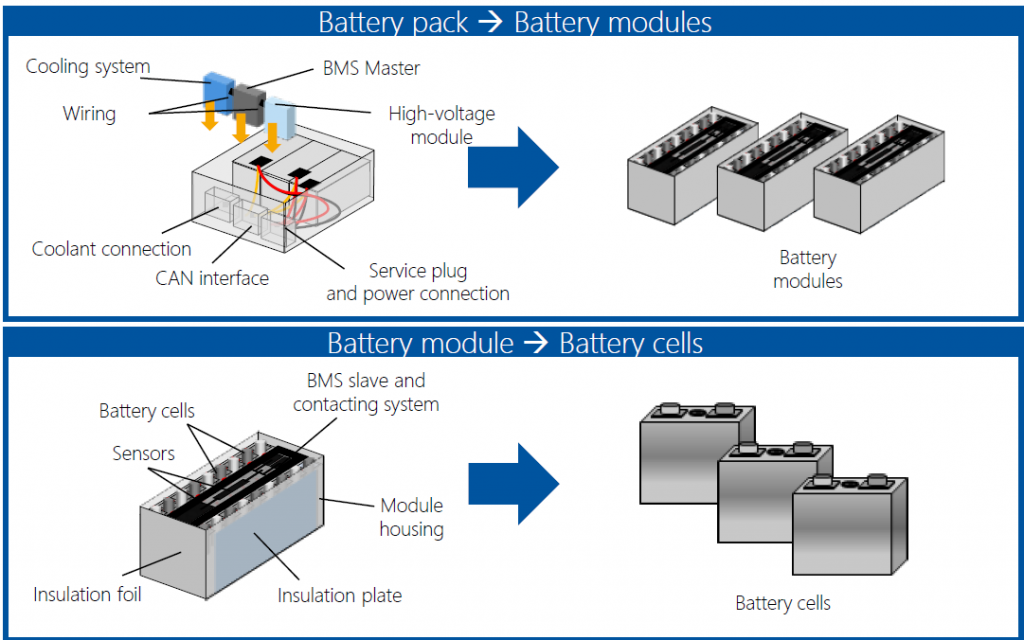
Source: startup-energy.org
Components Of A Lithium Car Battery Pack
- Cooling System: the cooling system removes heat from the battery modules and maintains a steady internal battery temperature.
- Battery Modules: a sub-unit that contains the battery cells.
- High Voltage Module: this brings together the power from all the battery modules.
- BMS Master: the BMS is the brain of a battery pack. It contains electronic circuitry and software and takes signals from sensors located in the battery pack. It also communicates with the vehicle’s computer system, providing data on the battery pack.
- Wiring: electrical wiring connects various components of the battery pack.
- Plugs And Connectors: these allow external power and communications cables to interface with the battery pack.
- Housing: this protects the battery pack from sunlight, heat, mechanical shock, or other stresses.
The battery cell is, without a doubt, the heart of the battery. Let’s have a look at its components.
Core Components Of A Battery Cell
- Anode: anodes attract lithium ions during a charge cycle. Graphite is typically the primary anode material.
- Cathode: cathodes attract lithium ions during the discharge cycle. Cathodes are typically made from aluminum foil coated with metal oxide.
- Separator: the separator physically separates the cathode and anode, avoiding a short circuit. It’s usually made from polypropylene or polyethylene and other plastics.
- Electrolyte: the electrolyte allows ions to flow back and forth between the cathode and anode. Electrolytes are typically made from a liquid, a polymer, or a solid-state material.
What Materials Are Lithium Car Batteries Made Of?
As shown above, many components go into lithium car batteries. As such, battery manufacturers need a wide range of materials. For recycling, the most valuable materials include:
- Lithium
- Manganese
- Nickel
- Cobalt
- Aluminum
Unquestionably, cathodes contain the most valuable materials and are usually the focal point of recycling activities. Cathodes vary in their design and composition, blending metals but always including lithium:
- Nickel manganese cobalt oxide, or “NMC.”
- Cobalt oxide, or “LCO.”
- Manganese oxide, or “LMO.”
- Iron phosphate, or “LFP.”
- Nickel cobalt aluminum oxide, or “NCA.”
The following image depicts the typical ratio, by weight, of these different cathode designs.
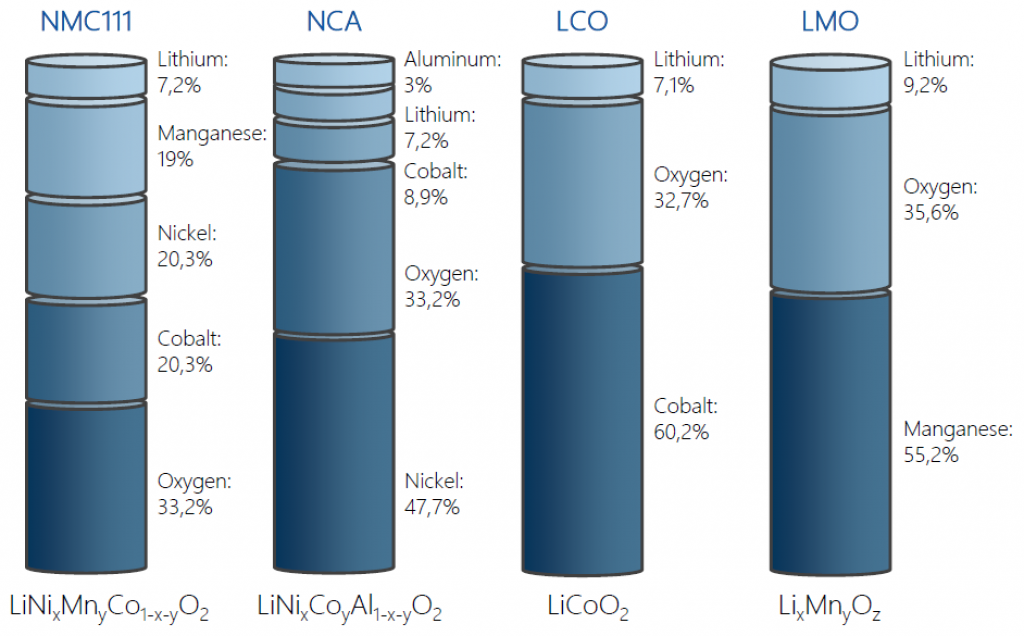
Source: startup-energy.org
Anodes are less valuable than cathodes but also contain valuable materials. The following materials are available in anodes:
- Graphite
- Silicon-graphite
- Silicon
- Lithium
Can Lithium Car Batteries Be Recycled?
Yes, the technical basis of recycling lithium car batteries is well established. At present, large-scale lithium-ion battery recycling is common in China and South Korea.
For example, China now has 25 industrial-scale battery recyclers. Experts cite that the current global lithium battery recycling capacity is around 250,000 tons per year.
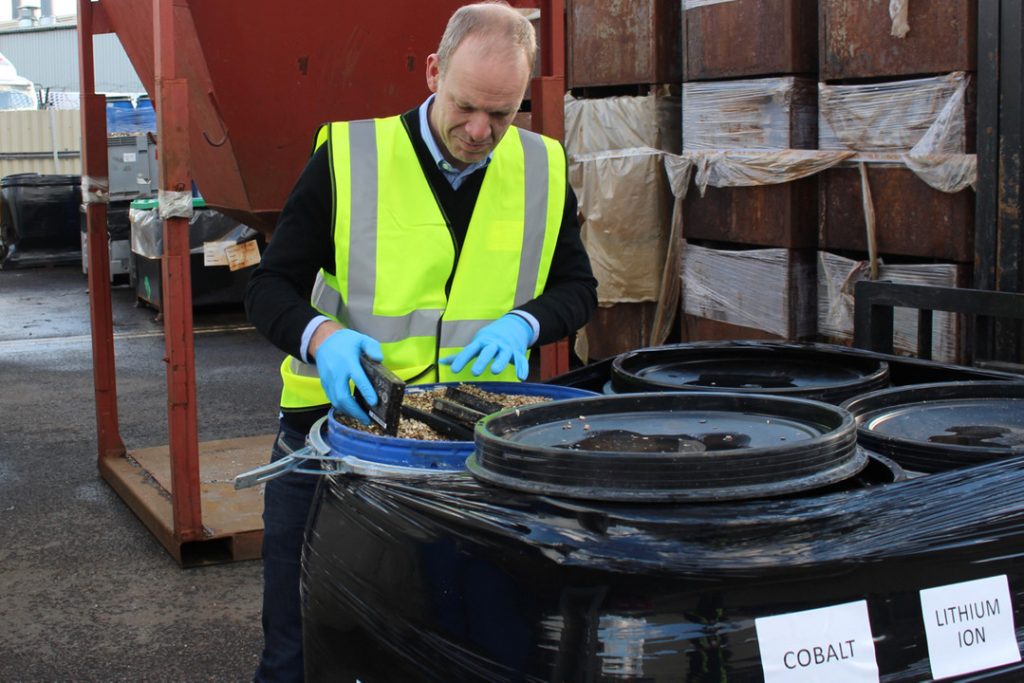
Can Lithium Car Batteries Be Reused?
In short, yes. So-called ‘second life’ batteries are lithium car batteries that can find a new life, usually stationary batteries.
Project developers deploy these reused batteries in stationary applications, like at wind farms or solar farms. Stationary applications are ideal for these batteries because battery energy density is not essential for stationary applications.
For example, the Swedish energy company Vattenfall installed 22 MW of BMW i3 batteries at the Pen y Cymoedd Wind Farm in South Wales, United Kingdom.
How To Recycle A Lithium Car Battery
You’ll recall that a wide range of valuable metals goes into batteries. As a result, recycling lithium car batteries aims to extract these valuable metals into a form useful to battery makers.
With this in mind, the primary recycling product is lithium carbonate. Other metals (in oxide form) are also extracted.
Chemical engineers designed these processes to extract these valuable metals at scale and cost-effectively.
In Summary
We can divide the recycling of lithium car batteries into three broad methods:
- Hydrometallurgy (using water/liquids)
- Pyrometallurgy (using heat)
- Direct Recycling
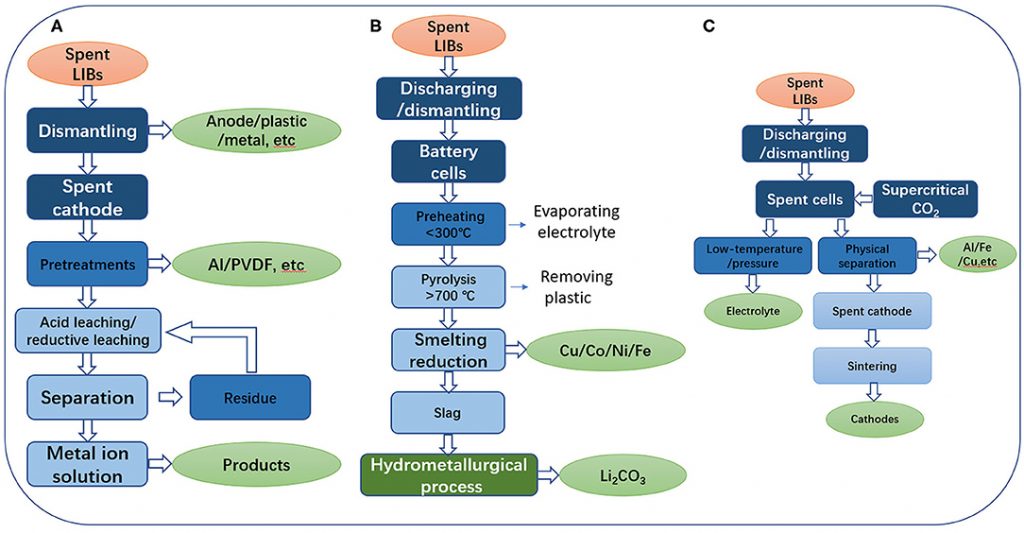
Source: Frontiers In Chemistry, Zhou, et al., 2020.
Although these are the broad categories of recycling methods, each battery recycler has a slightly different process; they are taking advantage of a particular business or expertise. What’s more, researchers are busy finding new and improved methods of recycling batteries.
Nevertheless, the objective is always to extract lithium carbonate and separate the various metal oxides — remember, cathodes are a blend of multiple metals.
In the following sub-section, we’ll examine the three battery recycling methods.
Process 1: Hydrometallurgy
Hydrometallurgy uses liquid-based processes to separate and extract various metals.
- Dismantle The Battery: separate battery cases, electrodes, and membranes containing electrolytes.
- Pre-treatment: the battery is fully discharged and either subjected to a solvent or shredded.
- Acid Leaching (or biological leaching): leaching removes certain metals from the overall mixture of metals. An acid solution, or micro-organisms, dissolves a metal from the mixture. The target metal can then be separated from the other metals.
- Precipitation: the various metal solutes are treated to precipitate the target metals.
- Filtering And Evaporation: a mechanical filter separates the lithium carbonate and metal oxides. An evaporator then removes the liquid, leaving lithium carbonate powder.
Process 2: Pyrometallurgy
Pyrometallurgy uses heat-based processes to separate and extract various metals.
- Dismantle: separate battery cases and cells, and discharge the battery.
- Pre-heat: this evaporates the electrolyte from the battery cells.
- Calcination: heat to above 1300°F to remove plastics
- Smelting: smelting involves heating the material to a high temperature in the presence of an oxidizing agent; this recovers non-lithium metals.
- Leaching Process: this extracts lithium carbonate from the remaining material using leaching. The lithium carbonate dissolves into the solution, whereas the other metal oxides remain in solid form.
- Filtering And Evaporation: a mechanical filter separates the lithium carbonate and metal oxides. An evaporator then removes the liquid, leaving lithium carbonate powder.
Process 3: Direct Recycling
Direct recycling allows the recycling of lithium batteries without high heat or chemicals. The objective is to minimize damage to the cathode microstructure.
- Dismantle: discharge batteries and separate battery cases, electrodes, and membranes containing electrolytes.
- Chill: supercritical CO2 extracts the electrolyte from the battery cells, allowing reuse.
- Separation: non-lithium metals are physically removed from the battery cells.
- Shred: shredders turn the electrodes into fine granules, which may or may not be further processed. For example, froth floatation can further extract materials.
Comparison Of Each Method
The following table summarizes the advantages, disadvantages, and recovery rates of the three primary recycling methods.
Hydrometallurgy | Pyrometallurgy | Direct Recycling | |
---|---|---|---|
Advantages | High recovery efficiency | High recovery efficiency | Low energy, low environmental impact Good potential for recycling LFP |
Disadvantages | Toxic by-products | Highly energy intensive Toxic gases produced | May not match raw material properties |
Recovery rate in % | 70 to 98% | 80 to 98% | 80 to 90% |
How To Reuse A Lithium Car Battery
Several companies now offer ‘second life’ batteries, repurposing car batteries for stationary applications.
The following section outlines how second-life battery companies inspect, test, and then grade their incoming old lithium batteries.
The process occurs in stages; if the inspectors accept a battery pack, they will not demand further testing or grading.
- Pre-Sort: inspectors examine and test batteries to classify and sort them, depending on their condition.
- State of Health (SoH) Test: the inspector conducts an SoH check, tests the battery pack, module, and cell, and assigns an SoH. The SoH is a number ranging from 0 to 100%.
- Grading And Disassembly: packs, modules, and cells are graded based on their SoH. The grading follows the following process:
- For a battery pack or modules with an SoH of 80% or above, the battery can be immediately used for second-life applications.
- Modules with an SoH of between 70% and 80% are suitable for building battery packs.
- For an SoH of less than 70%, modules are dismantled and then graded at a cell level.
- Battery cells with an SoH of more than 85% are used to build new battery modules.
- Cells, modules, and packs with an SoH that is too low are sent off for recycling.
- Re-Assembly: based on the SoH grading, cells, modules, and packs are re-assembled and deployed in a second-life application.
Final Thoughts
To sum up, the growth in the electric vehicle industry means a greater demand for lithium car batteries, exceeding global supplies. Therefore, recycling lithium car batteries is the only feasible way to meet this demand.
Lithium car battery recyclers already operate at a large scale, and the industry will continue to grow.